April 11, 2025 – A report released by Bank of America analyst Wamsi Mohan’s team this Wednesday highlights the potential hurdles Apple could face if it moves all iPhone production to the United States. According to the analysis, such a move could lead to a staggering 90% increase in production costs and create significant logistical challenges.
The primary obstacle to achieving “Made in USA” status for iPhones is the high cost of labor, which is projected to drive up the price of the devices by 25%. Additionally, the U.S. currently lacks a sufficient workforce skilled in smartphone assembly.
Another major challenge lies in the supply of components. Even if Apple could assemble enough workers for manufacturing in the U.S., a significant portion of the necessary parts would still need to be imported from China.
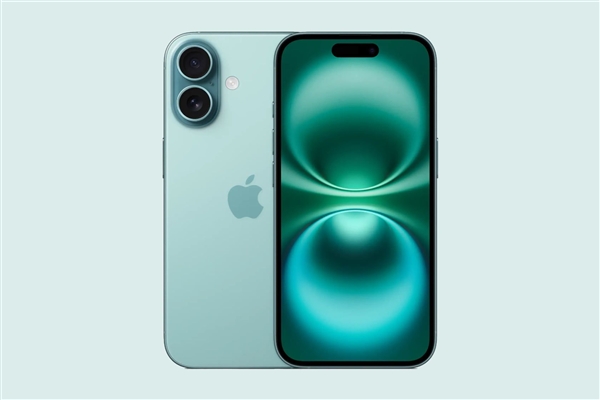
Should these imported components be subject to high tariffs, Apple’s overall costs could skyrocket by over 90%. This scenario would not only strain the company financially but also complicate its supply chain management.
Rosenblatt Securities has warned that tariffs could severely impact Apple’s stock price, while Wedbush analyst Dan Ives has lowered his target price, citing the trade war as a potential “disaster” for the company. Over the weekend, concerns about rising prices led to a surge in iPhone purchases as consumers rushed to buy before potential price hikes.
Mohan believes that for Apple to pursue final assembly of iPhones in the U.S., it would require tariff exemptions for components and sub-assemblies, a prospect he deems highly unlikely. “Apple will not move production to the U.S. unless the long-term nature of new tariffs is clear,” he stated.